With the growing demand for both higher quality and safer products, hemming sheet metal is becoming an increasingly common operation at the press brake. And with so many press brake hemming solutions on the market, determining which solution is right for your operations can be a project in itself.
Read below to learn more about the different types of hemming tools, or explore our Hemming Series and receive expert advice on the best hemming tool for your needs!
Explore Hemming Series
What is sheet metal hemming?
Just like in the garment and tailoring business, hemming sheet metal involves the folding of one layer of material over another in order to create a soft or rounded edge. It is used in a wide variety of industries including refrigeration, cabinet making, office equipment manufacturing, food processing equipment, and shelving and storage equipment just to name a few.
Historically, hemming has typically been used on materials ranging from 20 ga. through 16 ga. mild steel. However, with recent improvements in available hemming technology it is not uncommon to see hemming done on 12 – 14 ga., and in rare cases even as thick as 8 ga. material.
Hemming sheet metal products can improve aesthetics, eliminate exposure of sharp edges and burrs in areas where the part would otherwise be dangerous to handle, and add strength to the finished part. Choosing the right hemming tools depends on how frequently you will be hemming and which material thicknesses you plan to hem.
Hammer Toolshammer-tool-punch-and-die-hemming-process
Max. material thickness: 14 gauge
Ideal Application: Best for when hemming is performed infrequently and with little variance in material thickness.
Universal Bending: No
Hammer tools are the oldest method of hemming. In this method, the edge of the material is bent with a set of acute angle tooling to an included angle of approximately 30°. During the second operation, the pre-bent flange is flattened beneath a set of flattening tooling, which consists of a punch and die with flat faces to create the hem. Because the process requires two tooling setups, hammer tools are best reserved as a budget-friendly option for infrequent hemming operations.
Max. material thickness: 16 gauge
Ideal Application: Best for occasional hemming of thin materials. Ideal for “crushed” hems.
Universal bending: Yes, but limited.
The combination punch and die (or U-shaped hemming dies) utilize a 30° acute punch with a flattening jaw on the front and a U-shaped die with a wide flat surface at the top. As with all hemming methods, the first bend involves creating a 30ۡ° pre-bend. This is achieved by the punch driving the material into the U-shaped opening on the die. The material is then placed on top of the die with the pre-bend flange facing upward. The punch is again driven downward into the U-shaped opening on the die while the flattening jaw on the punch progresses through the flattening stage.
Due to the fact that the U-shaped hemming die has a solid wall of steel beneath the area where the flattening operation occurs, the high load capacity provided by this design works very well in creating “crushed” hems. Due to the use of an acute punch for the pre-bend, U-shaped hemming dies can also be used for universal bending applications.
The tradeoff to this design is that as the flattening jaw is located on the front of the punch, it must be fairly shallow in depth to avoid interference with the material as it swings upward to create the 30-degree pre-bend. This shallow depth makes the material more prone to slip out of the flattening jaw during the flattening stage, which can cause considerable damage to the press brake’s back gauge fingers. Typically, this should be an issue unless the material is galvanized steel, has any oil on the surface, or if the pre-bent flange is bent to an included angle that is greater (more open) than 30°.
Two stage hemming dies (spring-loaded)spring-loaded-hemming-process
Max. material thickness: 14 gauge
Ideal Application: For infrequent to moderate hemming applications of various material thicknesses.
Universal Bending: Yes
As press brakes and software increased in capability, two stage hemming dies became very popular. When using these dies, the part is bent with a 30° acute angle punch and a hemming die with a 30° acute angle V-opening. The upper sections of these dies are spring loaded and during the flattening stage, the pre-bent material is placed between a set of flattening jaws on the front of the die and the upper flattening jaw is driven downward by the punch during the stroke of the ram. As this occurs, the pre-bent flange is flattened until the leading edge comes into contact with the flat sheet.
While fast and highly productive, two stage hemming dies have their drawbacks. Because they use a spring loaded top, they must have enough spring pressure to hold the sheet without dropping even the slightest until the first bend begins. If they fail to do so, the material could slip beneath the back gauge fingers and damage them as the first bend is made. Furthermore, they require a V-opening that is equal to six times the material thickness (i.e., for material with a thickness of 2mm, spring loaded hemming dies require a 12mm v-opening).
Dutch bending tables / hemming tablesDiagram-of-Dutch-bending-table-hemming-process
Max. material thickness: 12 gauge
Ideal Application: Ideal for frequent hemming operations.
Universal Bending: Yes. The most versatile option for both hemming and universal bending.
Undoubtedly, the most modern and most productive progression of hemming tooling is the “Dutch bending table,” which is also referred to simply as a “hemming table.” Much like the spring-loaded hemming dies, Dutch bending tables feature a set of flattening jaws on the front. However, unlike the spring-loaded hemming dies, the flattening jaws on a Dutch bending table are controlled via hydraulic cylinders. The hydraulic cylinders make it possible to hem a wide variety of material thicknesses and weights because the issue of spring pressure is eliminated.
Doubling as a die holder, Dutch bending tables also feature the ability to interchange 30-degree dies, which also contributes to their ability to hem a wide variety of material thicknesses. This makes them extremely versatile and results in a dramatic reduction in set-up time. Having the ability to change the v-opening, combined with the ability to use the hydraulic cylinders to close the flattening jaws also makes it possible to use the system as a die holder when not in use for hemming applications.
Hemming thicker materialsMoving-flattening-bottom-tool-with-rollers
If you’re looking to hem materials thicker than 12 ga., you will need a moving flattening bottom tool. A moving flattening bottom tool replaces the traditional bottom flattening tool used in a hammer tool setup with a die that has roller bearings, which allow the tool to absorb the side load created in a hammer tool setup. By absorbing the side load the moving flattening bottom tool allows materials as thick as 8 ga. to be hemmed on a press brake. If you’re looking to hem materials thicker than 12 ga., this is the only recommended option.
Ultimately, no one hemming tool is suitable for all hemming applications. Choosing the right press brake hemming tool depends on which materials you plan to bend and how frequently you will be hemming. Consider the gauge range you plan to bend, as well as how many setups will be required to complete all necessary jobs. If you’re unsure of which hemming solution is best for your operations, contact your tool sales rep or WILA USA for a free consultation.
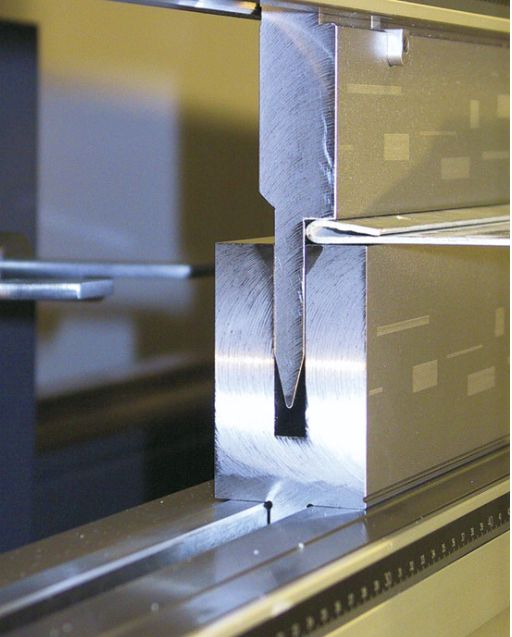
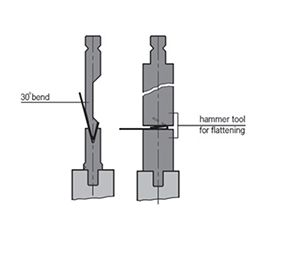
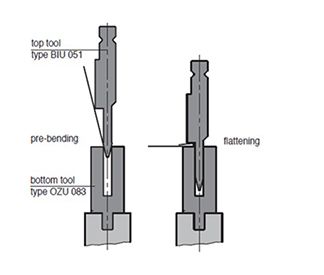
Post time: Aug-12-2022